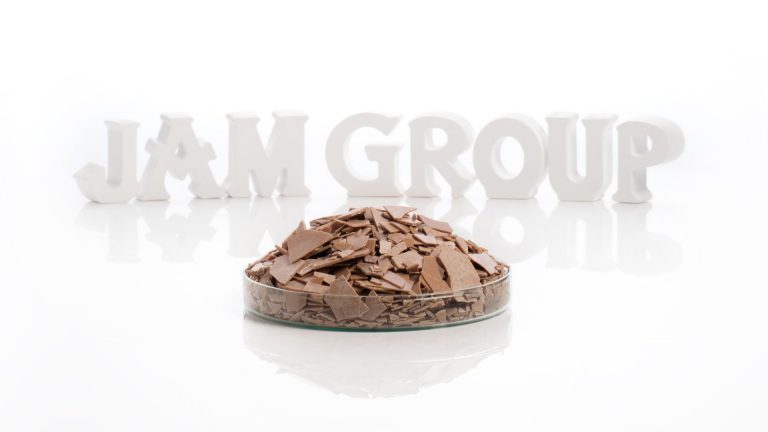
Sodium Hydrosulphide
As a multifunction chemical product, Sodium hydrosulfide has left footprints in diverse industries. This is a more robust product than Na2S, employed as a leather chemical substance, a reducing agent,
As a multifunction chemical product, Sodium hydrosulfide has left footprints in diverse industries. This is a more robust product than Na2S, employed as a leather chemical substance, a reducing agent,
Sodium Formate with the chemical formula of HCOONa, is the sodium salt of formic acid, HCOOH. It usually appears as a white deliquescent powder. JAM Group Co., is honorably able
Caustic soda, so-called lye or sodium hydroxide in the industry, is an inorganic chemical compound with the formula NaOH. The manufacturing of numerous daily things frequently uses this chemical as
Sodium Sulphide (Na2S) – Yellow Flake or “Zirnikh,” composed of the Na2S formula, is a multipurpose substance. This chemical compound is utilized in the manufacture of rubber chemicals, sulfur dyes,
One of the most cost-effective strategies to eliminate exposure to poisonous products or pose other hazards is to substitute currently used products with less hazardous ones. Any product, substance, or
From the dim and distant past, people covered themselves in dried animal pelts and removing the rotted parts of the skin was a problem. However, ways of processing and preserving the skins were discovered. The first solution was drying the skin with the sunlight. Washing with water and drying through fire was the second way. Later it was discovered that certain twigs, barks and leaves could be added to water in the soaking stage. Such discoveries were going on till the time being.
Nowadays, tanning is performed through scientific methods as is seen in the following.
JAM GROUP CO. is honorably able to supply all the needed chemicals in almost all the stages of leather processing such as Soaking, Depilation and Opening Up the Skin, Deliming, Bating, Degreasing, Pickling of Pelts, Tanning and Retanning, Neutralization (Deacidification) of Leather, Retanning, Bleaching and Fixation, Fatliquoring, Finishing, Water-Repellent Treatment of Leather, Drum Dyeing & Drying. In the following a general list of JAM GROUP’S leather chemicals is presented.
table
BATING AGENTSEnzymatic bating agents used in beamhouse stage
SODIUM SULPHIDE | Na2S – Yellow flakes with low Fe content. |
BASIC CHROME SULPHATE | Cr2(SO4)3 – Green Powder |
FORMIC ACID 85% SUBSTITUTION | An eco-friendly acidic product which is a great substitution for Formic Acid 85% in pickling, dyeing and tanning processes. |
LIMING AUXILIARIES | Products used to improve de-hairing and reduce the consumption of Na2S. |
DEGREASING AGENTS | Products used in deliming process of beamhouse stage
|
DEGREASING AGENTS | Eco-friendly APEO & NPEO free degreasing with high solid content
|
PRESERVATIVES & FUNGICIDES | Anti-bacterial agents based on PCP and Fungicides with different formulations |
TANNING & RETANNING AGENTS |
|
FATLIQUORS | Fully/semi synthetic, fully/semi natural and combination of different oils for different articles such as garments, upholstery, shoe upper, nappa and etc. |
FINISHING AUXILIARIES | Different products for finishing stage to achieve desired effects on the finished leather
|
The main goal for performing Soaking stage is restoring the natural condition of the skin and removal of dirt.
a. Soaking pits which is mainly used for pre-soaking of the dried skins
b. Paddle which is applied for careful soaking of delicate skins in long floats
c. Drum which is the most common method predominantly for heavy hides.
a. Mechanical treatment such as dry-drumming and breaking.
b. Temperature increase
c. Sharpening with alkalis
d. Sharpening with acidic chemicals
e. Common salt addition
f. Addition of soaking auxiliaries and wetting agents
g. Additions of enzymatic products like Basozym S 20
The main objective for performing this stage is removal of hair or wool and epidermis. Loosening up of the collagen fibre texture and partial saponification of the natural grease (which is equal to opening up of the skin and liberation of tanning-active groups.) are the other effects of depilation and opening up the skin.
a. Painting on the flesh
side (by hand or machine). This method is used when the hair or the wool are precious and we want to use them in other industries. The painting is performed on the flesh side to loosen the roots of the hairs without seriously damaging them.
b. Painting on the grain side
This way is used for special types of skin to produce a peculiarly smooth and fine grain leather. It should be mentioned that the hair is completely destroyed by using this method.
c. Drum painting
The lime paint is allowed to act first in a very short float and subsequently in an extended float (transition to drum liming).
a. Pure sulfide lime liquor
This method is performed with liming chemicals such as sodium sulfide and sodium hydrosulfide on leathers with very flat, closed grain. All the hairs are destroyed.
b. Pure white lime
This method is performed with liming chemicals such as hydrated lime powder (calcium hydroxide) and seldom slaked lime (lime paste) for reliming and seldom for long liming of soft leathers (gloving). It is a great method for loosening of the hairs and also opening up of the skin.
c. Combined sulfide and hydrated lime liquor
This is the most common liming process method.
d. Oxidative liming
This method is performed with liming chemicals such as sodium chlorite in conjunction with acid. It leads poor opening up of the skin.
a. Cold and warm sweating
This seldom used method is based of deliberate putrefaction process through enzymes. Hair-loosening is effected by the formation of enzymes and ammonia.
b. Enzymatic liming
This method is performed with specific enzymes, which attack the prekeratin of the roots. Using this method, the hair-loosening is also affected. To reach the optimum efficiency, alkaline preplumping or reliming is necessary.
The main objective of Deliming stage is removal of mechanically deposited lime and also chemically bound capillary lime by conversion into easily soluble salts.
The main objective of Bating stage is loosening of the texture of the skin and elimination of alkali-swelling by using specific enzymes.
Enzymes in bating agents
Enzymes are biological catalysts which accelerate the reactions without getting consumed during the reaction. proteases are those enzymes, which operate specifically on proteins.
The below proteases are applied as bating agents:
1. Pancreas proteases (trypsin)
2. Mould fungus proteases
3. Bacteria proteases
Pancreas proteases based bating agents which are the most popular enzymes indicate their optimum effect in slightly alkaline pH range (8.0 – 8.5).
Mould fungus proteases based bating agents show their best performance at pH 3.5 – 5.0, and bacteria proteases based bating agents have their best proficiency at pH 6.0 – 7.2.
Some commercial bating agents are made up of a mixture of all three types of proteases.
It is notable that the most effective bating temperature is 30 – 37 °C. Higher temperatures may cause damage to the skin.
The enzyme value is the number of enzyme units in 1 gram bating agent. One enzyme unit is the enzyme quantity which has fermentative capacity to digest 1.725 mg casein which is shown by LVU.
The enzyme unit is determined according to Löhlein-Volhard by allowing the bating agent to perform on an alkaline casein solution. Undigested casein is precipitated with hydrochloric acid and sodium sulfate. The consumption of alkali in re-titration is a direct calculation of the enzymatic effectiveness of the bating agent.
Pancreas-based bating agents which are predominantly used in practice:
1. Weak bating agents = 500 – 1000 LVU
(technical leather, harness leather)
2. Medium strong bating agents = 1000 – 1500 LVU
(upper leather, lining leather, fancy leather)
3. Strong bating agents = 1500 – 2000 LVU
(glove, clothing leather)
Degreasing methods
1. Wet degreasing of pelts and moist leathers
a. Squeezing out under high pressure.
b. In drums with wetting agents or emulsifiers.
c. In drums with fat solvents in combination with wetting agents or emulsifiers.
2. Dry degreasing of leather
a. Treatment with solvents in some specific degreasing plants with redistillation of the solvent.
b. Cleaning leather clothes by particular machines (dry cleaning) with solvents and specific detergents known as solvent soaps (surfactants) in case of need.
The main objective of Pickling is acidification of the pelts to a certain pH before chrome tannage and therefore, to reduce the astringency of the chrome tanning agents. Preserving is the other reason of performing the pickling stage.
Pickling methods
a. Salt-containing pickling systems
b. Low salt pickling systems
c. Short pickling methods
The main objective of Tanning and Retanning stages is to impart irreversible stabilization to the skin substance which is prone to putrefaction. The main goal of converting pelt into leather by tanning is to
● stabilize it against enzymatic degrading and increase its resistance to chemicals,
● increase its shrinking temperature and raise its resistance against hot water,
● reduce or eliminate its ability to swell,
● enhance its strength properties,
● lower its density by isolating the fibres,
● reduce its deformability,
● reduce its shrinkage in volume, area and thickness,
● enhance the porosity of its fibre texture.
These effects are attained by cross-linking the collagen chains with various tanning agents.
1. Vegetable tannage
a. Pit tannage
b. Accelerated tannage
c. Rapid tannage
2. Mineral tannage
a. Chrome tannage (wet blue tannage)
b. Aluminium tannage
c. Zirconium tannage
3. Other tannages
a. Aldehyde tannage (wet white tannage)
b. Oil tannage (chamois)
c. Immergan A tannage
4. Combination tanning methods
The above tanning methods are used in diverse combinations with one another and in different intensities to produce special leather properties. The dominating tanning method generally determines the final leather character.
Vegetable tanning is one of the most ancient tanning methods, and it is still an appealing option for manufacturing of some special types of leather. However, nowadays surely chrome tanning is the most important tanning method. Almost 80% of the worldwide produced leathers have been tanned by chrome.
An increasing amount of produced leather, especially automotive leather, is tanned with a mixture of aldehyde and synthetic/vegetable/polymer tanning agents.
Retannage becomes more important every day. It expands the size of production to industrial scale and improve the quality of the leather drastically. Syntans, resin and polymeric tanning agents are applied in retanning processes to adjust the character of the leather and improve its quality.
The classical classification of the tanning process to Tanning – Neutralization – Retanning is valid only for mineral tanning processes. Because the low pH after tanning has to be increased in order to allow a level distribution of the retanning materials (vegetable, synthetic, polymeric tanning agents). In purely organic tannages with vegetable tanning agents, syntans, aldehydes and polymers a prominent distinction between tanning and retanning is no longer possible.
AMOUNTS OF TANNING AGENTS REQUIRED FOR VARIOUS TYPES OF LEATHER
(Percentages on the pelt weight)
(Acid-forming) (Phlobaphene-forming)
Oak wood Quebracho
Chestnut wood Hemlock bark
Myrobalans Mimosa bark
Valonea Oak bark
Trillo Uranday wood
Sumac Tizera wood
Dividivi Mangrove
Galls Gambir
Acorn galls Cutch
Tara
Pine bark (mixture of pyrogallol-catechol)
MINERAL TANNING
Structure of mineral tanning agents
OTHER TANNING METHODS
Wet white tannage
Definition: Contrary to wet blue
Variation A: Free of heavy metals and aluminium salts.
Variation B: Free of chromium, but Al, Zr, Ti, Fe are accepted.
Wet white which is manufactured through pure organic tanning becomes more important every day. In such process the wet white is produced by mixture of:
Aldehydes
Syntans and vegetable tanning agents
Polymers
Auxiliaries
The characteristics of the leather are mostly manipulated by the amount and type of the applied syntan and also the parameter of the process. Thus, a diverse range leather could be produced, such as:
Automotive leathers
Upholstery leather
Garment leather
Shoe upper leather
It is notable that shavings and cuttings of wet white leather are free of chrome.
OIL TANNAGE
This is a particular tanning method using unsaturated oils for an extremely soft leather which is called chamois leat.
The main objective of this stage is to remove free acids present in the mineral tanned leather. For this reason, moderate auxiliaries are applied which do not lead to any damage on the leather.
Scientifically this process should be called deacidification and not neutralization. Since most of the times, the treatment of the leather is not reached to the neutral point.
Procedure
Neutralization is performed according to the type of the desired leather. To produce sof leathers severe neutralization throughout the whole cross-section is essential. Neutralization to only a certain depth of the cross-section is needed for firmer leathers.
In some cases, leathers are treated only with slight neutralizing syntan-like auxiliaries instead of alkalis.
Overneutralizing could be harmful for the leathers and must be avoided, otherwise a coarse loose grain and an empty handle are gained.
Most of the chrome tanned leathers need to be retanned. Some of the retanning agents have a strong dependency to the collagen and because of that are increasingly applied in metal free compound tannages.
Bleaching methods
1. Pelts and leathers tanned with formaldehyde, aluminium and fish oil
a. Oxidation bleach:
1. Potassium permanganate/sodium bisulfite
2. Hydrogen peroxide
3. Sodium chlorite
b. Reduction bleach
2. Vegetable/synthetic tanned leather
3. Chrome leather
a. Treatment with pale-tanning agents.
b. Sodium thiosulfate/acid treatment (deposition of colloidal sulfur).
c. Bleaching the leather by deposition of insoluble white salts. Pretreatment with barium chloride or lead acetate and after-treatment with sulfuric acid or magnesium sulfate or by deposition of titanium dioxide.
The main objective of this stage is to coat the fibre elements dehydrated during tanning by a fat layer to give leather the desirable softness and handle by a sort of lubrication. Simultaneously, fatliquoring affects the other physical properties of the leather, such as extensibility, tensile strength, wetting properties, waterproofness and permeability to air and water vapour.
The main fatliquoring materials:
A. Biological fatty substances
1. Vegetable oils
a. Drying oils: linseed oil, hemp oil, poppy oil, nut oil, wood or tung oil. (Limited use)
b. Semi-drying oils: colza or rape oil, maize oil, sunflower oil, soya bean oil, cotton seed oil, rice oil.
c. Non-drying oils: olive oil, castor oil, ground nut oil (arachis oil), fruit kernel oils.
2. Vegetable fats
Coconut fat, palm kernel fat, palm oil fat, Japan tallow.
3. Animal oils
a. Marine animal oils: seal oil, whale oil, dolphin oil (no technical use) Fish oils: herring oil, sardine oil, menhaden oil Liver oils: cod liver oil, shark liver oil
b. Land animal oils: neatsfoot oil, lard oil
4. Animal fats
Beef and mutton tallow, lard, butter fat, bone fat, horse grease.
5. Waxes
a. Vegetable: carnauba wax, candelilla wax, montan wax.
b. Animal: beeswax, wool grease.
B. Non-biological fatty substances
Paraffin waxes, mineral oils, olefins, processed hydrocarbons, synthetic fatty acid esters and waxes, fatty alcohols, alkyl benzenes.
1. Untreated oils, fats and waxes
2. Emulsified oils and fats
3. Sulfonated oils, fats and fatty alcohols
a. sulfated products
(-C-O-S bond, ester-like, splittable)
b. sulfonated products
(-C-S bond, true sulfo acid, unsplittable)
4. Chlorinated oils and fats
a. chlorinated products
b. sulfochlorinated products
5. Oxidation products of oils and fats
6. Hydrolysis products of oils and fats
FATLIQUORING METHODS
1. Oiling-off (mainly for sole leather)
2. Cold stuffing on the table
3. Hot stuffing by the dipping process
4. Fatliquoring (principal method)
a. fatliquoring in warm aqueous float
b. fatliquoring in cold aqueous float
c. dry fatliquoring (without float)
d. oiling by brush
ANALYSIS OF LEATHER FATLIQUORING AGENTS
1. Water-insoluble fatliquoring agents
a. Determination of water content
b. Determination of non-volatile, non-fatty organic substances
(The insolubles in ether minus ash give the non-volatile, non-fatty
substances)
c. Determination of total volatile substances
(Water and organic solvents)
d. Determination of content of mineral matter
e. Fatliquoring substances
(Product weighed out minus water, volatile and non-volatile organic
substances and mineral matter)
f. Determination of fatty acids
g. Determination of unsaponifiable matter
2. Water-soluble fatliquoring agents
a. Determination of fatliquoring substances
(100 minus water, mineral matter and volatile organic substances = % fatliquoring substances)
b. Separation into emulsifying and emulsified components
(according to Panzer-Niebuer)
Emulsified proportion = neutral fat, unsaponifiable matter, free fatty acids (in petroleum ether solution)
Emulsifying proportion = emulsifiers (in aqueous/alcoholic solution)
c. Testing for sulfonation
d. Determination of degree of sulfonation
(total SO3, inorganically and organically bound SO3)
e. Determination of degree of neutralization
f. Determination of neutral salts in sulfonated oils
The main objective of this stage is to enhance the interfacial tension between leather fibres and water and as a result declining or almost completely removal of the wettability with water by depositing water-repellents in the leather substance.
Hydrophobic = water-repellent
Oleophobic = oil-and-dirt-repellent
Chemical classification of leather dyes
1. Nitro and nitroso dyes
2. Metallized and non-metallized azo dyes
a. monoazo dyes
b. polyazo dyes
3. Diphenyl and triphenyl methane dyes
4. Sulfur dyes
5. Phthalocyanine
6. Anthraquinone and multi-ring dyes
7. Natural dyes
Classification of leather dyes according to their application properties
1. Anionic dyes
a. acid dyes
b. direct (substantive) dyes
c. special dyes
d. dyes that can be dispersed in water
2. Cationic dyes
3. Oxidation dyes
1. Drum dyeing (drum, mixer, three-chamber automatic dyeing machine)
a. Dyeing in hot float
The most frequently used method.
b. Dyeing without float (dry or powder dyeing)
To accelerate penetration. To reach great levelness of the shade, the temperature should not exceed 25 °C.
c. Dyeing in steps (sandwich dyeing)
Depth of shade is improved by adding acid or cationic dyeing auxiliary between two dye additions.
d. Effect dyeing
Production of cloudy, patchy or marbled dyeings with two- or multitone effects.
e. One-side drum dyeing
Reverse side resisting with special polymer products.
2. Paddle dyeing
Dyeing in long floats. Mainly used for dyeing wool sheep skins to prevent felting of the wool.
3. Dyeing in the through-feed machine (Multima)
Dip dyeing of crust leather; very short immersion time in dye liquor.
4. Colouring by curtain coater
5. Colouring by roll coater
6. Colouring by screen printing
A printing paste is pressed by means of a squeegee onto the leather through a fine screen with a negative pattern (mono- or multicoloured).
7. Spray staining
Application of dye solutions through compressed air spraygun. Depth of penetration is regulated by the addition of organic solvents or penetrators.
8. Tray dyeing and brush staining. Methods only seldom used nowadays.
Drying methods for leather
1. Air-drying without supply of energy (hang-drying)
2. Air-drying with supply of energy
a. air circulation method (hang-drying)
b. drying in channel, tunnel, chamber (hang-drying)
c. wet-toggled drying
d. paste drying
3. Hot water drying
a. Secotherm process (paste drying)
4. Infrared drying
5. Vacuum drying
6. High-frequency drying
Brightening dyes
Used together with pigment finishes of high covering power or alone in top coating mixtures to enhance the brilliance of plate and glaze finishes or of spray and brush stained shades.
The brightening dyes should meet the following requirements:
• compatibility with finishing agents,
• good light fastness,
• fastness to bleeding and hot plating,
• good fixing properties,
• fastness to alkali and formaldehyde,
• low content of extenders.
1. Water-soluble or water dilutable brightening dyes
Chiefly the Eukesolar Dyes 150 Liquid are used and to a less extent selected anionic dyes of the Luganil and Luganil Liquid ranges or colour lakes (about two parts anionic dye stirred together with one part of basic dye in dissolved form at boiling temperature).
2. Solvent-soluble brightening dyes
Eukesolar Dyes 150 Liquid
Copyright © 2024 Jam Group Company. All rights reserved.