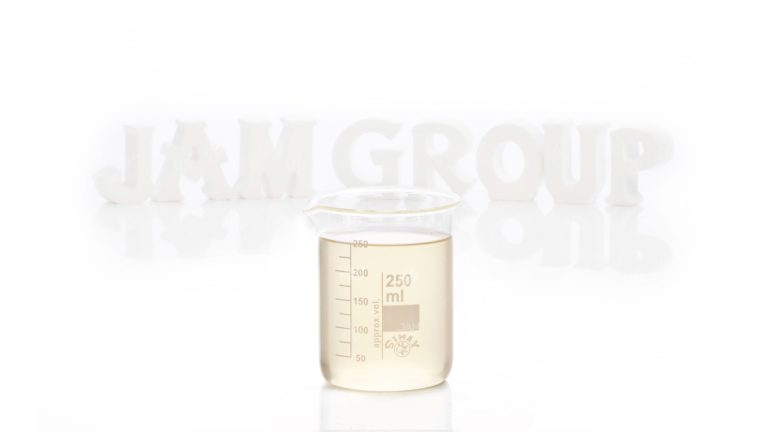
Spin Finish Oils
Spin finish oils are liquid compositions with components such as Lubricants, emulsifiers, and antistatic agents. These products widely function on the surfaces of man-made fibers to optimize their processing in
Spin finish oils are liquid compositions with components such as Lubricants, emulsifiers, and antistatic agents. These products widely function on the surfaces of man-made fibers to optimize their processing in
Caustic soda, so-called lye or sodium hydroxide in the industry, is an inorganic chemical compound with the formula NaOH. The manufacturing of numerous daily things frequently uses this chemical as
The textile industry holds a vital position in the global economy, contributing significantly to both employment and manufacturing outputs. Central to this industry’s success are textile chemicals, which play a pivotal role across various stages of the textile value chain. From the initial processing of fibers to the final finishing of fabrics, these chemicals are essential. They enhance properties like durability, colorfastness, and comfort, ensuring textiles meet both functional and aesthetic requirements. Whether it’s during dyeing, printing, or coating, textile chemicals adapt textiles to diverse applications, underscoring their indispensable nature in producing quality fabric products. This article is dedicated to discussing different types of textile chemicals and how they are applied in this industry’s value chain. We start this task by having a look at the textile industry and the different stages involved in it; then, we will move on to the main topic and review crucial types of chemicals employed in these stages.
Before moving on to the topic of textile chemicals, we’re going to talk about a prominent manufacturer, supplier, and exporter of textile chemicals of various types. JAM Group Co., a renowned entity in the textile chemical sector, operates two fully-equipped factories staffed with seasoned chemists. Their commitment extends beyond manufacturing, as they provide standard packaging and a variety of transportation options to ensure global accessibility. Emphasizing environmental responsibility, JAM Group Co. offers an array of pure textile chemicals, ensuring minimal ecological impact. Customers worldwide trust them for secure packaging and dependable delivery of their products. To assist with specific requirements, including pricing, JAM Group’s team of experts is readily available to offer guidance and support, reinforcing their status as a reliable partner in the textile industry.
Understanding the textile industry and its multiple departments is a vital precursor to discussing textile chemicals. From humble beginnings in homespun workshops to the complex processes of modern times, the textile industry has woven a rich tapestry throughout history. As a cornerstone of human civilization, this industry has been pivotal in dressing the world, creating a spectrum of fabrics from delicate silks to durable types of denim. Its evolution has been marked by key technological milestones, such as the flying shuttle and the spinning jenny, which multiplied the threads of output. The revolutionary strides continued with the power loom, enhancing fabric creation, and reached new efficiencies with the advent of the steam engine, cotton gin, and the sewing machine. Today, the textile sector is a vast, intercontinental network that begins in the fields and farms, nurturing natural fibers or delving into the earth for minerals to synthesize futuristic fabrics.
In this modern era, the textile industry represents a nexus of art and science, marrying aesthetics with innovation. It is not merely a chain of production but a web of creativity and technology. This industry extends far beyond the mere fabrication of material; it is the backbone of fashion, the herald of trends, and a testament to human ingenuity in meeting the ever-changing demands of comfort and style. From pastoral beginnings with the rearing of sheep and cultivation of silkworms, to the high-speed textile mills that pulse with the rhythm of machinery, the industry has grown in complexity and scope. It is a world where traditional techniques coexist with cutting-edge advancements, ensuring the legacy of textiles continues to enfold the future.
This labyrinthine industry encompasses myriad processes that take place in various departments of the textile industry. In the following, we will discuss them in detail. It helps us understand the role of textile chemicals more profoundly.
The journey of yarn manufacturing has its roots in ancient times. Early humans discovered that by twisting short fibers together, they could create a continuous thread. Initially, this was a slow and challenging process. To make it easier, simple tools were developed for sorting and arranging the fibers. This led to the invention of primitive carding tools, which helped to organize the fibers according to their length.
Over time, as technology advanced, the methods of yarn formation also evolved. Silk fibers were drawn out from cocoons, and synthetic fibers were created through chemical processes. Today, we have sophisticated systems that can blend both staple and filament fibers, allowing for a wide variety of yarns. These modern techniques are the backbone of the textile industry, providing the yarns that are essential for creating diverse and functional fabrics.
Yarn formation is a critical process in the textile industry, where fibers, either natural or synthetic, are transformed into yarns. Natural fibers, such as cotton and wool, go through several steps before they become yarn. These steps include:
Synthetic fibers, however, offer different possibilities. They can be turned into filament yarns that are long and continuous or cut into staple lengths similar to natural fibers for spinning. Whether natural or synthetic, these fibers are then twisted together, forming the yarns used in making a wide range of fabrics.
Textile chemicals are not typically involved in the core process of fabric formation, which primarily focuses on the physical methods of constructing fabric. Still, forming fabric is a vital process that we must discuss.
Fabric formation is a pivotal stage in the textile industry, where yarns are transformed into fabrics through various methods, the most common being weaving and knitting. Weaving, a process employed for about 70% of the world’s fabrics, involves interlacing two distinct sets of yarns known as the warp and the weft. This is typically done on a loom, which holds the warp threads in tension while the weft threads are woven through them at right angles. The resulting fabric can vary in texture and strength based on the type of weave used, which includes plain, satin, and twill weaves. Each weaving method imparts different characteristics to the fabric, making it suitable for a range of applications from clothing to home furnishings. Weaving is versatile, accommodating various materials like cotton, wool, silk, and synthetic fibers like nylon. The precision and structure of woven fabric make it a staple in the textile industry, catering to both functional and aesthetic needs.
In contrast, knitting offers a different approach to fabric formation. Unlike weaving, where yarns intersect at right angles, knitting involves interlocking loops of yarn in a series of rows and columns, known as courses and wales, respectively. This method creates inherently stretchable fabrics, providing comfort and adaptability to the body’s movements. Knitted fabrics are widely used for items like sweaters, hosiery, and underwear, thanks to their ability to trap air, making them warm and absorbent.
Fabric finishing is another crucial and varied stage in the textile production process, where textiles, whether they be yarns, woven fabrics, knits, or ready-to-wear items, undergo various treatments to acquire desired properties and aesthetics. This stage is not a single, uniform step but a collection of diverse processes tailored to the needs of the final product. These processes can include washing, bleaching, printing, and coating, each serving a specific purpose. For example, washing improves cleanliness and texture, bleaching can alter the fabric’s color, and printing adds patterns or designs.
Additionally, finishing techniques can impart functional properties such as softness, soil repellency, shrink resistance, and even flame retardancy. The choice and sequence of these finishing processes depend greatly on the end-use of the textile product, making this phase highly customizable. This flexibility allows for a wide range of finished textiles, each meeting specific consumer requirements, and showcases the textile industry’s capacity to adapt and innovate according to the diverse demands of the market.
All in all, we can classify all the stages involved in fabric finishing under three main categories:
It is an essential first step in the fabric finishing process, particularly for fabrics destined for dyeing, printing, or other finishing treatments, except for specific types like denim and certain knits. During pretreatment, mills focus on removing any natural impurities or processing chemicals from the fabric that might hinder subsequent finishing processes. This includes not only residues from the fabric’s own manufacturing journey but also any agricultural residues that might have adhered to natural fibers. Mills typically use a standard set of pretreatment equipment for all their products, though the exact steps can vary depending on the fabric and fiber type involved.
The process encompasses several key treatments, and various textile chemicals are applied to them. They include mechanical ones like cutting, minting, brushing, and singeing, which prepare the fabric’s surface. Desizing and scouring further clean the fabric, removing size agents and other impurities. Other steps like carbonizing, which removes vegetable matter from animal fibers, bleaching for color removal, mercerizing to increase strength and luster, and surface modifications, are chosen based on the specific requirements of the fabric.
Coloring processes in fabric finishing represent the transformation of textiles through the addition of color, a critical aspect of textile appeal and functionality. At its core, coloring involves the application of colorants – textile chemical substances containing chromophoric groups that interact with light, creating the perception of color. The process of coloring can be broadly classified into a few main techniques.
Each coloring technique, whether it’s bleaching, dyeing, or printing, plays a pivotal role in defining the final look and feel of the textile product, catering to the diverse preferences and requirements of consumers and designers alike.
In the textile industry, the finishing stage is where textiles are endowed with their final desired properties, both in terms of aesthetics and functionality. Various types of textile chemicals are employed in this crucial stage. It encompasses a variety of treatments that may be mechanical, physical, or chemical in nature. Mechanical treatments often utilize chemical agents to enhance or sustain their effects, including processes like calendering, which smoothens the fabric, and sanforizing, which controls shrinkage. Chemical treatments vary; some involve a chemical reaction with the fiber, while others, like softening treatments, do not. For instance, waterproofing and flame-retardant finishes involve adding chemicals that fundamentally change the fabric’s properties, making them suitable for specific end-uses.
On the other hand, treatments like emerising, which gives a suede-like finish, focus on the textile’s tactile quality. The objective of these finishing processes is to achieve specific characteristics, whether it’s creating a unique look and feel or enhancing the functional aspects of the textile, like strength or resistance to environmental factors. Each treatment is carefully selected based on the fiber type and the intended use of the textile, ensuring that the finished product meets the required standards and consumer expectations.
Textile chemicals are a diverse group of organic and inorganic substances used in the transformation of both natural and synthetic fibers into finished textile products. These chemicals play a vital role in enhancing the textiles to meet specific customer needs and end-use requirements. They are integral in various stages of textile production, from the initial treatment of fibers to the final finishing touches on a fabric. For example, during the dyeing process, chemicals are used to ensure that colors are vibrant and long-lasting.
Similarly, in the finishing stage, chemicals can be applied to give fabrics unique properties like water resistance, flame retardancy, or enhanced durability. These chemicals are essential in achieving the desired quality and functionality in textiles, making them attractive and suitable for a wide range of applications, from clothing and upholstery to industrial uses. The careful selection and use of these chemicals are crucial for not only meeting consumer expectations but also adhering to environmental and safety standards in the textile industry.
In the following, you can read more about different types of textile chemicals and their particular applications across the textile chain.
These are a crucial category of textile chemicals designed to enhance the interaction between water and solid materials like fabrics. Their primary function is to reduce the surface tension of water, enabling it to spread more easily across the surface of textiles or penetrate the fibers. This is achieved through the use of surfactants, substances that have both hydrophilic (water-attracting) and lipophilic (oil-attracting) properties. When applied to textiles, the hydrophilic part of the molecule adheres to the fabric, while the lipophilic part faces outward, facilitating the formation of a continuous phase between the liquid and the solid material. This principle of wetting is fundamental in various textile processes.
Wetting agents are known for their resilience to different conditions, such as varying pH levels and hard water. They are highly soluble in water and provide several benefits, like improved penetration, even dyeing, and effective dispersion. Additionally, these agents play a significant role in preventing issues like color bleeding and uneven spots during dyeing. They are also instrumental in enhancing the smoothness, dispersion, and adhesion of other products like glues, adhesives, and paints used in textile applications.
Textile sizing chemicals are a group of water-soluble polymers essential in strengthening and protecting yarn during the weaving process. Commonly used agents include modified starch, polyvinyl alcohol (PVA), carboxymethyl cellulose (CMC), and acrylates. These sizing chemicals are chosen for their strong adhesive qualities, suitable viscosity, and excellent molding capabilities, ensuring they effectively coat and protect the yarn. Stability in both physical and chemical properties is crucial, as is their ability to dissolve and disperse in water, facilitating ease of application in textile processing. The sizing process involves soaking the fabric in a slurry of these sizing agents, often combined with preservatives, and then drying it to achieve a thicker, stiffer feel. This slurry may also contain softeners, fillers, or fluorescent brighteners, depending on the desired outcome.
Natural pastes like wheat starch and cornstarch are traditional sizing agents, but more contemporary formulations often include components like CMC, PVA, and polyacrylate. The application of sizing typically involves dipping or rolling the fabric in the sizing solution, followed by a two-stage drying process. This critical process enhances the fabric’s quality, preparing it for further manufacturing steps and ensuring its durability and suitability for end-use.
Wax removing agents, also known as wax cleaning agents, are specialized nonionic, colorless liquids used predominantly in the pretreatment phase of textile processing. These agents are adept at eliminating oil and wax stains from fabrics, making them particularly suitable for use on pure cotton materials. Their primary advantage lies in their ability to efficiently remove wax, a common issue in cotton and hemp textiles, where wax spots can hinder waterproofing and dyeing processes, potentially leading to defects in the final product.
Wax removing agents stand out due to their excellent dispersing, emulsifying, and washing capabilities, which are essential for treating various fabrics during scouring and bleaching processes. Their high resistance to alkali makes them versatile in different fabric treatment scenarios. Moreover, these agents improve the water absorption capacity of yarn and fabric, which is especially beneficial for high-density fabrics, enhancing their wool effect and laying a solid foundation for subsequent dyeing processes. While wax removal is just one part of the comprehensive pretreatment process in textile manufacturing, it plays a vital role in ensuring the evenness of dyeing or printing and in enhancing other fabric qualities, such as whiteness and softness.
Textile softeners, a key category of textile chemicals, play an essential role in enhancing the feel and comfort of fabrics. Among these, cationic surfactants are particularly effective due to their strong adsorption capabilities on fiber surfaces. These surfactants align tightly and uniformly on the fiber, resulting in a significantly softer texture. The primary function of textile softeners is to reduce the fabric’s stiffness, which can occur due to various processing steps in textile manufacturing. By softening the fibers, these agents make the final textile product more pleasant to touch and wear. This quality is crucial for a wide range of textile products, from everyday clothing to luxury fabrics.
Soaping agents in textile processing play a vital role in ensuring the cleanliness and clarity of dyed fabrics. At their core, these agents contain surfactants, which are key to their effectiveness. Surfactants in soaping agents are responsible for dispersion, emulsification, and solubilization, which are crucial for removing excess dye and impurities from the fabric. Anionic surfactants, such as sulfonates, sulfates, carboxylates, and phosphates, are commonly used for their strong cleaning abilities. Additionally, nonionic surfactants, which may include compounds like polyethylene glycol groups and polyoxyethylene fatty acid esters, contribute to the gentle yet effective cleaning action of these agents.
Another group of textile chemicals are called retard agents, specifically flame retardants, which are crucial in enhancing the safety of textiles by reducing their flammability. These agents function by disrupting the combustion cycle of textile fibers, which typically involves thermal cracking, oxidation, and the release of heat. One key metric for assessing flammability is the Oxygen Index (LOI), which indicates the minimum concentration of oxygen needed for combustion. Flame retardants work through several mechanisms:
Mercerizing agents, a crucial type of textile chemicals, play a pivotal role in enhancing the quality of cotton textiles. This process involves treating cotton goods, such as yarn or fabric, with a concentrated caustic soda solution while maintaining tension, followed by a thorough washing to remove the solution. The result is a significant improvement in the fabric’s properties: it becomes smoother, more absorbent, and chemically reactive, which enhances dye uptake. Mercerizing also improves shrinkage rate, dimensional stability, and flatness, along with altering strength and extensibility.
Anti-staining agents are textile chemicals used in the textile industry to prevent unwanted dye transfer during the dyeing and printing processes. These agents can be broadly categorized based on their mechanical and chemical properties. Mechanically, substances like waxes, oils, and certain inorganic compounds are used to create barriers on fabrics, preventing dyes from coming into contact with the fibers. Chemically, various acids, bases, salts, oxidants, reductants, and specific compounds like phenylhydrazine sulfonic acid work to either neutralize dyes or form precipitates, inhibiting staining. Common applications include coating fabrics with materials such as paraffin, turpentine, or clay to shield them from dye contact. Others interact directly with dyes to mitigate their staining potential, using agents like lime or aluminum sulfate. These anti-staining agents are particularly beneficial for maintaining the original appearance of white cotton fibers and ensuring that the fabric’s quality is not compromised during processes like acid or neutral stone washing.
In textile washing, anti-precipitation agents play a crucial role, particularly when using detergents like direct chain alkylbenzene sulfonate Sodium (LAS). While LAS is cost-effective and produces abundant foam, its solubility issues, especially at lower temperatures, can lead to the formation of white precipitates, causing product instability and separation. Anti-precipitation agents, such as sodium toluene sulfonate, sodium xylene sulfonate, urea, ethanol, and isopropanol, are added to resolve this problem.
These agents enhance the solvent properties of the wash, ensuring even distribution and preventing unwanted precipitation. These textile chemicals significantly improve the dyeing process, shortening dyeing time for blended fabrics, preventing staining due to their dispersion properties, and aiding in the removal of surface dyes from fibers. It leads to enhanced fabric fastness and a better hand feel. Furthermore, their ability to keep the bath clean and residue-free makes them indispensable in maintaining the quality and consistency of textile washing processes.
JAM Group Co. has established itself as a leading manufacturer and supplier in the textile chemical industry. It offers a diverse range of products, including Antistatics, Spin finishes, Softeners, Dispersing Agents, Waxes, and Anti-foams. The company operates two state-of-the-art factories, one located in Eastern Europe and the other in the Middle East. These facilities are not only well-equipped but also staffed with experienced chemists, ensuring that JAM Group consistently delivers high-quality textile chemicals to the international market. Their commitment to excellence and extensive range of products have positioned them as a trusted name in the textile chemical sector.
In addition to its production capabilities, JAM Group Co. excels in the transportation and delivery of its products. The company is dedicated to ensuring the safe and standard-compliant packaging of its chemicals, adhering to international norms for safety and quality. Furthermore, JAM Group offers tailored transportation solutions and shipping options, catering to the diverse needs of its global clientele. This comprehensive approach to logistics guarantees that customers, regardless of their location, can confidently rely on the timely and secure delivery of JAM Group Co.’s products, further cementing the company’s reputation as a dependable partner in the textile industry. Feel free to read more about this company by navigating to About Us.
Later on, you can get to know the company’s products in detail.
JAM Group Co. specializes in providing various grades and types of antistatic agents, ensuring the highest purity and efficacy for synthetic fibers. These antistatics are integral components of the ‘spin finish’ applied to fibers just after they emerge from spinnerets. This finish, containing lubricants and antistatic agents, is crucial for the high-speed processing of modern fibers, aiding in yarn production, knitting, weaving, and the manufacture of non-woven materials. While these agents fulfill their purpose during initial processing stages, they are typically removed during fabric preparation. JAM Group also offers non-durable antistatics for technical textiles that don’t undergo regular washing, such as filters, conveyor belts, and transport bands. These products are essential for reducing static buildup, ensuring smooth operation and longevity of both the textiles and the machinery used in their production.
JAM Group Co. excels in providing a range of Spin Finishes, which are essential textile chemicals for the processing of man-made fibers. These spin finishes, available in various grades and types, are crafted to the highest standards of purity. Applied as either a liquid or solid composition to the surfaces of synthetic fibers, these finishes significantly enhance the fibers’ performance in both short-staple and long-staple spinning operations. By improving the handling and processing characteristics of these fibers, JAM Group’s spin finishes ensure smoother production runs and higher quality in the final textile products. Their spin finishes are designed to meet the diverse needs of modern fiber processing, offering solutions that boost efficiency and quality in textile manufacturing.
JAM Group Co. offers a diverse range of softeners, available in various grades and types, formulated with the utmost purity. These softeners are integral finishing agents applied to textiles to impart a pleasant and comfortable feel. Serving as lubricating agents, they facilitate the sliding of fibers within the fabric, making it easier to deform and crease, thereby enhancing the fabric’s handle. JAM Group’s softeners can be applied at different stages of textile processing, including during washing and rinsing, as well as before or after dyeing. Their range includes non-ionic, anionic, and cationic surfactants, silicone-based, and reactive softeners, each chosen for their specific effects on the fabric’s feel and texture.
JAM Group Co. also offers an extensive range of dispersing agents, another group of textile chemicals, all crafted to the highest purity standards, essential in the textile dyeing process. These agents, often non-ionic surfactants like alkyl-polyethylene glycol, are crucial for creating stable dispersions of low-solubility dyes in water. Their primary function is to maintain the dye in a dispersed state, preventing aggregation and precipitation, which is key for achieving an even dyeing effect.
Commonly used dispersing agents in sulfur dyeing include naphthalene sulfonic acid–acid-formaldehyde condensate and lignin sulphonates. Additionally, these agents aid in enhancing dye solubility, ensuring a uniform distribution of color. JAM Group also incorporates anti-migration additives in their formulations to prevent dyestuff redistribution during the drying phase, a critical aspect known as migration. This attention to detail in their dispersing agent product line demonstrates JAM Group’s commitment to delivering quality and consistency in textile processing.
JAM Group Co. provides a range of high-quality textile waxes, vital for finishing yarns and enhancing their weaving process. These waxes, offered in various grades and forms, serve as hydrophobic treatments that not only ease and strengthen fibers but also contribute to maintaining gloss and improving abrasion resistance. The unique formulation of these waxes includes a blend of hydrocarbon wax, a mixer, and an emulsifier, ensuring that the waxed fabrics can resist water effectively, causing water droplets to form beads on the surface.
The emulsifier in the wax has adequate hydrophilic properties to make the waxed structure easily scourable, balancing its inherent hydrophobic nature. Beyond water resistance, the benefits of using JAM Group’s textile waxes include improved tear resistance, fabric softening, enhanced heat setting, and reduced needle cutting in the fabrics. This versatility and effectiveness, coupled with growing eco-friendly awareness and technological advancements, drive the global market demand for textile waxes, positioning JAM Group as a key player in this sector.
Copyright © 2024 Jam Group Company. All rights reserved.