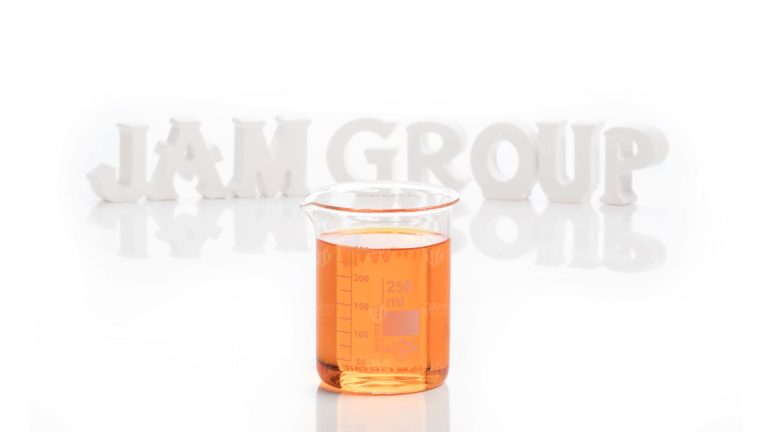
Sodium Isopropyl Xanthate (SIPX)
Sodium Isopropyl Xanthate (SIPX), a pure grade of Xanthate, holds various functions in several industries, especially in mineral processing. With its unique properties, this chemical compound is primarily used as
Sodium Isopropyl Xanthate (SIPX), a pure grade of Xanthate, holds various functions in several industries, especially in mineral processing. With its unique properties, this chemical compound is primarily used as
Methyl Isobutyl Carbinol (MIBC) is a colorless molecule with unique chemical and physical properties that lead to particular functions of this compound. As a chemical intermediary, MIBC has applications in
European alchemists first noticed soluble silicates of alkali metals (sodium or potassium) in the 1500s. Since then, these substances have played a vital role in various places. A common category
Potassium butyl xanthate (PBX) is a yellowish powder with a strong odor soluble in water and alcohol. With a molecular weight of 188.4 g/mol and the chemical formula C5H9KOS2, it
As a multifunction chemical product, Sodium hydrosulfide has left footprints in diverse industries. This is a more robust product than Na2S, employed as a leather chemical substance, a reducing agent,
With the chemical formula Na2SO3, sodium sulfite (also known as sodium sulphite) is an inorganic substance. It is a white, water-soluble substance that holds its unique physical and chemical properties
Caustic soda, so-called lye or sodium hydroxide in the industry, is an inorganic chemical compound with the formula NaOH. The manufacturing of numerous daily things frequently uses this chemical as
Sodium Sulphide (Na2S) – Yellow Flake or “Zirnikh,” composed of the Na2S formula, is a multipurpose substance. This chemical compound is utilized in the manufacture of rubber chemicals, sulfur dyes,
Mineral processing is a fascinating field that involves extracting valuable minerals from the earth and transforming them into useful products. One of the most crucial elements in this process is using various chemicals to aid in separating and purifying minerals. From froth flotation reagents like sodium ethyl xanthate and sodium isopropyl xanthate to other essential chemicals like zinc sulphate monohydrate, sodium hydrosulfide, and methyl isobutyl carbinol, each chemical plays a unique role in mineral processing. These powerful agents work together to extract the precious minerals and refine them to perfection, like a master alchemist creating a potion of gold. Without these essential chemicals, the mineral processing industry would be like a treasure hunter without his tools, unable to uncover the valuable gems hidden deep within the earth. In the following, you can find out more about mineral processing chemicals and their involvement in the process.
JAM Group Co. is a reputable Iranian manufacturer, supplier, and exporter of mineral processing chemicals that is dedicated to providing the highest quality products to its customers. As a leading supplier, producer, and trader of mineral processing chemicals in the Middle East, JAM Group Co. has established a reputation for delivering the finest chemicals to customers worldwide. With a focus on innovation and quality, JAM Group Co. is committed to continuing its tradition of excellence in the manufacture of mineral processing chemicals, making it a top choice for any company in need of reliable and effective chemical solutions. Whether you are a mining company looking to extract valuable minerals or a chemical enterprise needing specialized reagents, JAM Group Co. has the expertise and resources to deliver the perfect solution for your unique needs. Trust JAM Group Co. as your go-to source for all your mineral processing chemical needs.
Mineral processing chemicals are a range of chemical compounds that are used in the process of mineral separation and concentration. These chemicals are used to separate valuable minerals from non-valuable substances through various chemical reactions. They are typically employed in the stages of froth flotation. Some of the most common mineral processing chemicals include collectors, frothers, modifiers, and activators. Many producers worldwide tend to create these reagents. For instance, zinc sulphate monohydrate ZnSO₄ manufacturers (or, as Russian speakers put it, моногидрат сульфата цинка ZnSO₄ Производитель), china manufacturers of caustic soda, and potassium amyl xanthate (PAX) manufacturers usually provide these crucial materials.
Learning more about mineral processing chemicals, their importance, and their applications require a comprehensive understanding of mineral processing and its stages. Accordingly, we review each stage of this process in detail and then discuss mineral processing minerals. But first, we must familiarize ourselves with the collectors, frothers, modifiers, and activators as crucial materials in froth flotation; Below, you can find out more about them.
Collectors, also known as promoters, are an essential component in the froth flotation process. They are polar reagents with a metal ion on one end and an organic ion on the other. They play a crucial role in establishing a hydrophobic surface on the desired mineral, allowing it to attach to air bubbles and float to the surface. Collectors work by adsorbing onto the metal ions present on the surface of the mineral. The organic ion present at the other end forms a new surface that is hydrophobic. This allows the mineral to attach to the air bubbles and float to the surface, making it possible to separate it from the other minerals in the ore.
Many different types of collectors can be used in froth flotation, each with its own unique properties. These chemicals are effective in selectively separating different kinds of minerals and are widely used in the mining industry. Some common examples include:
Each company that is in demand of collectors must find a reputable producer of these chemicals to achieve the desired results. Some producers seek specific grades of these materials. In this case, they can easily rely on JAM Group Co., an Iran exporter of Sodium Sulphide flakes, which is also famous as a Sodium Sulphide yellow flakes Na2S 60% manufacturer, a reputable Iran manufacturer of sodium hydrosulfide, and a powerful Sodium Isopropyl Xanthate (SIPX) manufacturer.
Collectors are significant in separating complex ores where more than one type of mineral is present. By selectively attaching to certain minerals, they make it possible to separate them from the other minerals in the ore. It is essential in the mining industry, where the goal is to extract as much of the valuable mineral as possible while minimizing the amount of waste.
Frothers are a crucial component in froth flotation, as they play a vital role in the stability of the froth. Froth flotation is a method of separating valuable minerals from undesirable materials by creating a stable froth on the surface of a slurry. It is achieved by introducing small bubbles of air into the slurry, which attach to the desired minerals, causing them to float to the surface. Frothers are surface-active chemicals added to the slurry to prevent the bubbles from coalescing or bursting. They work by lowering the slurry’s surface tension, creating a more stable froth that can effectively separate the minerals. Without frothers, the froth would be unstable and unable to effectively separate the minerals.
There are different types of frothers available, including low molecular weight alcohols such as methyl isobutyl carbinol (MIBC) and high molecular weight alcohols, and pine oil. Each frother has unique properties, and the choice of frother will depend on the specific application and the separated minerals. Various producers, such as china manufacturers of Methyl isobutyl carbinol (MIBC) and Indian manufacturers of Methyl isobutyl carbinol (MIBC), are in the business. Still, we should consider Iranian manufacturers of Methyl isobutyl carbinol (MIBC) that provide this material in a variety of grades; trusting these companies, you can enjoy lower methyl isobutyl carbinol (MIBC) prices compared to the other producers.
Frothers are utilized in a variety of mineral processing industries, including the mining, metallurgy, and coal industries. They are also used in the recycling of paper and other materials. The use of frothers enables the efficient separation of valuable minerals, making the froth flotation process an essential tool in extracting and processing minerals.
Modifiers, also known as regulators, play a crucial role in the mineral processing industry by allowing for the selective separation of minerals through froth flotation. These chemicals are employed to alter the conditions of the slurry and minerals to achieve the desired outcome in the flotation process.
One of the primary uses of modifiers is to activate minerals that do not naturally float well, such as sphalerite. It is done by adjusting the slurry’s pH by using chemicals such as lime, soda ash, caustic soda, and sulfuric acid. These pH modifiers can also act as depressants, helping to separate certain minerals from the rest of the ore. It is worth mentioning that finding a reliable producer, for instance, a reputable caustic soda manufacturer is necessary to reach the intended results. Aside from Chinese, Indian, and Turkey manufacturers of caustic soda, JAM Group Co., a famous Iranian manufacturer of caustic soda, is a company that you can trust.
Modifiers also play an important role in counteracting the adverse effects of interfering substances such as slimes, colloids, and soluble salts that can absorb and reduce the effectiveness of flotation reagents. They can help to prevent these substances from attaching to the desired minerals and interfering with the flotation process.
In the froth flotation process, modifiers, collectors, and frothers are added to the slurry. The combination of these three types of chemicals is essential for achieving a successful separation of minerals. The use of modifiers allows for fine-tuning the conditions of the slurry and minerals, making it possible to achieve a high degree of selectivity and efficiency in the flotation process.
Activators are a type of mineral processing chemical used in froth flotation to enhance the flotation of certain minerals. They work by increasing the hydrophobicity of the mineral surface, making it more likely to attach to air bubbles and float to the surface. Zinc sulphate monohydrate ZnSO4 is one example of an activator. It is often employed to activate minerals such as sphalerite, which have a naturally low floatability. Finding a reputable zinc sulphate monohydrate ZnSO₄ Exporter (also known as çinko sülfat monohidrat ZnSO₄ İhracatçı in Turkish) that provides this activator in pure grades is vital.
Activators are different from frothers, collectors, and modifiers in that they do not directly affect the froth’s stability or the flotation process’s selectivity. As mentioned, frothers stabilize the froth and prevent air bubbles from coalescing or bursting, while collectors selectively establish a hydrophobic surface on the desired mineral. Modifiers, on the other hand, vary the conditions of the slurry and minerals to achieve a differential flotation. Activators simply work to enhance the floatability of certain minerals, making them more likely to float to the surface. Activators are used to improve the flotation of naturally hydrophobic minerals or with lower floatability. They are used in conjunction with other reagents, as they cannot achieve flotation on their own.
As mentioned in the previous section, discussing mineral processing chemicals requires a general knowledge of mineral processing and its vital stage, froth flotation. Mineral processing, also called ore dressing or mineral beneficiation, is a crucial step in the mining industry that involves extracting valuable minerals from the earth. It is a complex process that involves multiple stages, including crushing, grinding, and separation, to separate the valuable minerals from the waste rock. Techniques such as gravity separation, flotation, and cyanide leaching are employed to concentrate the minerals and separate them from unwanted materials. The ultimate goal of mineral processing is to produce a concentrate suitable for further refining or smelting that meets the market’s specific requirements.
Mineral processing has a long history, dating back to ancient times when manual labor and simple tools were used to extract valuable minerals from ore. Over time, more advanced methods and equipment were developed, such as stamp mills and mechanical devices like the Frue vanner. These machines played a significant role in increasing the efficiency and effectiveness of mineral processing. Today, the mining industry continues to rely on mineral processing to extract valuable minerals from ore and improve mining operations’ profitability.
The process of mineral processing is essential for the mining industry to extract valuable minerals from ore and make them available for everyday applications. The profitability of a mine is often determined by the amount of mineral concentrate that can be extracted from the ore and the quality of the concentrate that is produced. Before items are released onto the market, mineral processing is intended to produce the most mineral concentrate feasible. The process is constantly evolving as new technologies and techniques are developed to improve efficiency in response to changing industry conditions.
Mineral processing is crucial for extracting various materials. These materials include:
It is vital to note that each manufacturer of mineral processing chemicals should present specific substances based on the purpose of mineral processing and the producer’s intentions.
Mineral processing plays a crucial role in the mining industry as it enables the extraction of valuable materials from the earth. Each manufacturer of mineral processing chemicals in Iran performs this technique on a specific material, including metals, rocks, and industrial mineral ore, used in everyday applications such as construction, manufacturing, and energy production. Without mineral processing, it would be impossible to extract and purify these materials to the level required for commercial use. Additionally, mineral processing allows for separating valuable minerals from unwanted materials, resulting in a concentrate that can be further refined or smelted to create a final product. The efficiency and effectiveness of mineral processing directly impact the profitability of a mine, making it a vital component of the mining industry. As technology advances, mineral processing will become even more critical in increasing yields and reducing the environmental impact of mining.
Mineral processing is a critical step in the mining industry that involves a series of complex procedures to extract valuable materials from ores and other raw materials. The process starts with the extraction of minerals from the earth and ends with the final product being ready for use or sale. The different stages of mineral processing include crushing, grinding, sizing and classification, concentration, and dewatering. The different stages of mineral processing play a crucial role in achieving the desired outcome, and each step has its own set of importance. It is also vital to find a reliable exporter of mineral processing chemicals and provide all of the requirements in high quality and grade to ensure the outcome of the process.
Each of these stages plays a vital role in achieving the desired outcome and is essential to the overall efficiency of the mineral processing operation. Crushing is the first stage of the process, where large rocks and ores are broken down into smaller pieces. This is typically done using jaw crushers, cone crushers, and gyratory crushers. Grinding comes next, where the crushed materials are ground down into finer particles using various mills. Sizing and classification is the next stage, where the particles are separated into different size ranges and classified according to their mineral content. Concentration is the fourth stage, where valuable minerals are separated from unwanted materials through techniques such as flotation, gravity separation, and magnetic separation. During this stage, some producers rely on frothers, collectors, and modifiers created by china manufacturers of mineral processing chemicals. The final step, dewatering, is removing water from the concentrate to produce a dry, saleable product. In the following, you can discover more about each of these stages.
Mineral processing is a multi-stage operation that begins with crushing raw ore. This stage involves breaking down large chunks of ore into smaller, more manageable particles. To accomplish this task, various types of equipment are utilized, such as jaw crushers, gyratory crushers, and cone crushers. These machines use mechanical force and compression to effectively reduce the size of the ore.
One of the main goals of the crushing stage is to reduce the size of the ore, making it more manageable for subsequent processing stages. Additionally, this stage helps to expose valuable minerals within the ore, making them more accessible for further steps such as grinding, concentrating, and refining. The size reduction that occurs during the crushing stage also increases the surface area of the ore, which can be beneficial for certain processes like leaching.
Crushing is a critical step in mineral processing, as it serves as the foundation for the entire operation. This stage’s effectiveness can directly impact the efficiency and success of the overall process. Therefore, choosing the appropriate equipment and carefully adjusting its settings is essential to ensure the best possible outcome, otherwise, it results in an impure product that doesn’t fit the desired application and increases the producer’s costs. This problem becomes more crucial when we consider the mineral processing chemicals price and other potential charges. Factors to consider when selecting and setting up crushing equipment include the size of the equipment, the type of ore, and the desired end product.
The second stage of mineral processing is known as Grinding. This stage is crucial as it involves reducing the size of the ore particles to extract the valuable minerals contained within. The goal of this stage is to create a uniform and fine particle size that is suitable for further processing. There are several methods that can be employed for grinding, including ball mills, rod mills, and autogenous mills. Each method has its own advantages and disadvantages, and the choice of which method depends on the specific ore being processed. For example, ball mills are typically suitable for softer ores, while rod mills are better suited for harder ores. On the other hand, autogenous mills use the ore as the grinding media, making them particularly effective for processing very hard ores.
In addition to size reduction, grinding also serves another essential purpose: mineral liberation. It is the process of breaking down the ore particles to release the valuable minerals so they can be further processed. It is done by using grinding media to physically break down the ore particles, which can then be separated using flotation, which requires various mineral processing chemicals from Chinese, Indian, or Turkey manufacturers of mineral processing chemicals, such as Sodium Sulphide, sodium hydrosulfide, and Methyl isobutyl carbinol (MIBC).
The Grinding stage entails a significant amount of energy and can considerably contribute to the overall cost of mineral processing. As such, it is essential to optimize this stage in order to minimize costs while still achieving the desired particle size and liberation. It can be done by carefully selecting the grinding media, adjusting the mill operating conditions, and monitoring the performance of the grinding circuit.
The third stage of mineral processing, sizing and classification, plays a vital role in extracting valuable minerals from ore. This stage involves separating the desirable minerals from the waste materials, or gangue, based on their size and weight. It involves grinding the ore to a fine powder, a process known as comminution. The process is carried out using various types of equipment, such as mills, crushers, and grinders.
Once the ore is in fine powder form, it then goes through a series of screens and classifiers. Screens help to remove any oversized particles, while classifiers are utilized to separate the particles based on their weight and density. To separate the particles, these classifiers use various methods, such as hydro cyclones, spirals, and shaking tables. The heavier minerals, such as gold and silver, will be separated and collected, while the lighter materials will be discarded. This stage is crucial as it dramatically increases the concentration of valuable minerals in the final product, making it more economically viable to extract and sell. It also helps reduce the environmental impact of mining by limiting the waste material that must be removed.
The size and classification stage of mineral processing is also known as beneficiation. It is because it improves the quality of the ore by removing impurities and increasing the concentration of the valuable minerals. It is a critical step in the mining process as it separates the valuable minerals from the waste material and makes it more economically feasible to extract and sell. This stage results in a higher-grade ore ready for further processing.
Concentration is a vital stage in mineral processing as it is responsible for separating valuable minerals from the waste materials in the ore. This stage is crucial in ensuring that the final product is of high quality and contains a high concentration of the desired mineral. Without proper concentration, the efficiency and effectiveness of the entire mineral processing operation would be significantly reduced. Furthermore, choosing the appropriate technique and adjusting the settings is essential to ensure the best possible outcome. The equipment size, the type of ore, and the desired end product are all factors that must be considered when selecting and setting up the concentration equipment.
Several techniques are used in the concentration stage, each with advantages and disadvantages. Each method’s merits lead to various manufacturers’ usage of this technique; for instance, some producers decide to utilize froth flotation in this stage. In this case, they must find a reliable mineral processing chemicals producer, such as Iran manufacturer of Sodium sulphide red flakes, a sodium hydrosulfide manufacturer, or a methyl isobutyl carbinol (MIBC) manufacturer since these chemicals are crucial in this technique. Below, you can learn more about froth flotation and other methods.
One popular method is automated ore sorting, which uses optical sensors to sort the rock into different categories based on specific characteristics. This technology is continually advancing and is becoming more sophisticated as more sensing parameters are added.
Another technique that can be applied is electrostatic separation, which relies on electric currents to separate the desired mineral from impurities. Electrostatic separators and electrodynamic sensors, also known as high-tension rollers, are used in this process. It is important to note that the ore material must be dry for this technique to be effective.
It is another standard method used in concentration. It utilizes a chemical collector and frother, such as Sodium Sulphide, sodium hydrosulfide, Methyl isobutyl carbinol (MIBC), and Sodium Isopropyl Xanthate (SIPX), that creates bubbles on the surface of the slurry that hydrophobic materials bind to. These bubbles are then collected off the surface of the frother. Activators can be used to enable the flotation of one mineral ore, while depressants are used to inhibit the flotation of unwanted materials. It is also worth mentioning that each producer who wants to use froth flotation in the concentration stage must find a reliable Iranian, Chinese, or Indian manufacturer of mineral processing chemicals to ensure the quality of the chemicals used.
Gravity separation is also a popular technique that can be used in concentration. It separates two or more ore minerals in their respective responses to gravity paired with buoyant forces, centrifugal forces, or magnetic forces in a viscous substance. This process can be used to separate a wide range of minerals.
Magnetic separation can also be utilized in concentration. It involves using electromagnets to extract the desired mineral ore from a conveyor belt. This process can be used with or without water and can be particularly effective for separating certain types of minerals.
The concentration stage is critical when preparing the ore for further processing. It helps to expose the valuable minerals, making them more accessible for subsequent steps, such as grinding, concentrating, and refining. The size reduction achieved in the concentration stage also increases the surface area of the ore, which can be beneficial for certain processes like leaching.
Dewatering is an important stage in mineral processing that removes the water content of the mineral and allows for the separation of the valuable concentrate from the unwanted gangue. This stage is crucial for the marketability of the mineral as it helps to reach the desired concentrate levels for sale. The dewatering process can be accomplished through various methods, such as thickening, filtration, and drying. In thickening, the slurry is separated into the solid and liquid components, with the solid component being further processed. Filtration involves the use of filters to separate the solid and liquid components, while drying uses heat to remove the moisture content.
The choice of dewatering method depends on various factors such as the mineral type, particle size, and the desired final product. For example, thickening is often used for minerals with large particle sizes, while filtration is used for smaller particles. The efficiency of the dewatering process is also crucial as it directly impacts the final product quality and marketability. The use of advanced technologies such as centrifugation, vacuum filtration, and pressure filtration has improved the efficiency and cost-effectiveness of the dewatering process.
Froth flotation is a highly efficient method of mineral concentration that has been widely adopted in the mining industry. This process utilizes the unique properties of minerals to separate them from unwanted materials in the ore. By using chemical reagents, the surface properties of the desired mineral are modified, making them hydrophobic and allowing them to attach to air bubbles. These bubbles then float to the surface, where the hydrophobic minerals are skimmed off as a frothy concentrate.
One of the critical advantages of froth flotation is its ability to selectively separate minerals based on their physical and chemical properties. This property makes the method an ideal one for recovering valuable minerals such as copper, lead, and zinc sulfides and oxide minerals like hematite, cassiterite, malachite, and phosphates. Additionally, technological advancements have expanded the use of froth flotation to recover fine coal.
Regarding tonnages of ore treated globally, froth flotation is the most critical mineral recovery process. Using mechanical or pneumatic agitation tanks or cells generates air bubbles, providing the process’s physical aspect. The chemical aspect is supplied by reagents (such as zinc sulphate monohydrate (ZnSO₄), Potassium Amyl Xanthate (PAX), and caustic soda) that vary the surface properties of minerals and the slurry medium to enable the separation of valuable minerals from unwanted materials. In this case, manufacturers can rely on chemical flotation manufacturers (so-called kimyasal flotasyon üreticisi in Turkish) to find various grades of reagents.
Froth flotation is a complex process that requires careful control of the chemical and physical conditions to achieve optimal results. However, it can yield a high-quality concentrate ready for further processing when executed correctly. This makes it a crucial stage in the mineral processing industry and is one of the critical factors contributing to mining operations’ efficiency and profitability.
Flotation reagents, or mineral processing chemicals, are chemical substances utilized in one stages of mineral processing, froth flotation. These reagents play a crucial role in selectively separating valuable minerals from unwanted materials in the ore. By modifying the surface properties of the minerals, flotation reagents allow for the efficient extraction of valuable minerals and their preparation for further processing. Notably, three main types of surfactants are used in flotation: collectors, frothers, and modifiers. It is also vital to note that the proper use and selection of these reagents is critical to the success of the flotation process and can make a significant difference in the final product. In the following, you can read more about these mineral processing chemicals that are usually produced by reliable manufacturers worldwide (known as mineral işleme kimyasalları üreticisi in Turkish).
Collectors, also known as promoters, are polar reagents with a metal ion on one end and an organic ion on the other. They work by adsorbing onto a metal ion in the mineral surface, creating a new surface that is hydrophobic. It allows the desired mineral to preferentially adhere to air bubbles and float to the surface.
Frothers, on the other hand, are surface-active chemicals that help to maintain the stability of the froth by lowering the surface tension of the slurry. These chemicals prevent air bubbles from coalescing or bursting, making it difficult to separate the valuable minerals from the unwanted ones. Frothing properties can be persistent or non-persistent depending on the desired stability of the froth.
Modifiers, also known as regulators, vary the slurry and mineral conditions to assist in the selective flotation of minerals. These chemicals can activate poorly floating minerals, such as sphalerite, or depress certain minerals to perform a differential flotation on a complex ore. pH modifiers, such as lime, soda ash, and sulfuric acid, can also be used to control the alkalinity and acidity of the slurry, which can counteract the detrimental effects of slimes, colloids, and soluble salts that can reduce the effectiveness of flotation reagents.
JAM Group Co. is a leading Iranian manufacturer, supplier, and exporter of mineral processing chemicals (or, as Russian people phrase it, производитель химикатов для обогащения полезных ископаемых). With a focus on providing high-quality products to its customers, the company has established a reputation as a reliable source of reagents for the mining industry.
As a leading Iran supplier of mineral processing chemicals, JAM Group Co. offers a wide range of products for froth flotation, including:
As a leading Iran producer of mineral processing chemicals, JAM Group Co. produces these reagents in-house, ensuring consistent quality and timely delivery. Additionally, as a top Iran trader of mineral processing chemicals, JAM Group Co. exports its products to customers around the world, making it a significant player in the manufacture of mineral processing chemicals in the Middle East. Explore the About Us page for further insights into JAM Group Co.
As a reputable and prominent player in the Iranian mineral processing chemical industry, JAM Group Co. supplies top-notch reagents tailored to enhance the efficiency of the froth flotation process. The company’s portfolio comprises a diverse array of flotation reagents, such as sodium ethyl xanthate, sodium isopropyl xanthate, and zinc sulphate monohydrate, all of which are known for their exceptional performance in the separation of valuable minerals from impurities. Their cutting-edge formulas are designed to optimize the froth flotation process, making it a reliable and efficient method for mineral extraction. You can easily trust these products that hold a higher quality compared to other international producers, such as China’s manufacturer of Sodium Sulphide flakes and other chemicals.
In the following, you can gain an understanding of JAM Group’s mineral processing chemicals and their properties.
Sodium Sulphide, represented by the chemical formula Na2S, exists in two common forms: the anhydrous state and its hydrate Na2S·9H2O. These crystalline solids are typically colorless, but technical grades often display hues ranging from yellow to brick red due to the presence of polysulfides. Available in crystalline masses, flake forms, or as fused solids, sodium sulfide is water-soluble, producing strongly alkaline solutions. Exposure to moist air causes the release of hydrogen sulfide, an extremely toxic, flammable, and corrosive gas with a distinctive rotten egg odor. This compound, offered by JAM Group Co. in various grades and purities, finds applications across different industries.
In mineral processing, Sodium Sulphide (Na2S) plays a crucial role, particularly in froth flotation. Widely used in the flotation of oxidized copper, lead, and zinc minerals, sodium sulfide is instrumental in the sulfidization process, initially developed in the U.S.A. between 1915 and 1920 for oxide copper mineral flotation. This process is particularly effective for oxidized lead ores with basic gangue. Early users recognized the dynamic and delicate nature of the sodium sulfide reaction, understanding that its rate varies with factors such as temperature, soluble salts, and pH. JAM Group Co. offers Sodium Sulphide as a key player in mineral processing, ensuring varied grades and purity levels to meet the diverse needs of its customers in this critical industrial application.
Sodium Hydrosulfide, with the chemical formula NaHS, is a product resulting from the half-neutralization of hydrogen sulfide (H2S) with sodium hydroxide (NaOH). Industrially, sodium hydrosulfide and sodium sulfide find common use, often serving similar purposes. The colorless solid form of NaHS has an odor reminiscent of H2S due to hydrolysis by atmospheric moisture. Unlike sodium sulfide (Na2S), which is insoluble in organic solvents, NaHS, being a 1:1 electrolyte, exhibits greater solubility. In a solid flake state, sodium hydrosulfide is flammable, presenting a colorless or slightly off-white appearance with an odor similar to H2S. JAM Group Co. offers sodium hydrosulfide in various grades, ensuring diverse levels of purity to meet the requirements of its customers in mineral processing applications.
Sodium hydrosulfide (NaHS) emerges as a critical chemical in froth flotation, particularly in copper mining operations. Functioning as a flotation agent, NaHS activates oxide mineral species, serving as an effective means of sulfidizing oxide ores. Its primary application involves separating copper (Cu) from molybdenum (Mo), depressing the Cu from the Cu-Mo concentrate to enable conventional flotation metal separation. Sodium hydrosulfide plays a pivotal role in the mining industry, with copper mining constituting its second-largest end-use, consuming substantial quantities. In the ore froth flotation process, NaHS is utilized to beneficiate low-grade minerals, facilitating the separation of desired metallurgical minerals from waste material. This results in the formation of a recoverable froth where the valuable minerals float to the surface, contributing to efficient metal recovery.
Sodium Hydroxide, commonly known as caustic soda, is an inorganic compound denoted by the chemical formula NaOH. This white solid ionic compound is composed of sodium cations (Na+) and hydroxide anions (OH−). Renowned for its highly corrosive nature, sodium hydroxide acts as a potent alkali, capable of decomposing lipids and proteins at ambient temperatures, potentially causing severe chemical burns. With high solubility in water, it readily absorbs moisture and carbon dioxide from the air, forming various hydrates like NaOH·nH2O. The commercially available sodium hydroxide often presents as the monohydrate NaOH·H2O, especially in the temperature range of 12.3 to 61.8 °C. This versatile chemical finds applications across multiple industries, including wood pulp and paper production, textiles, drinking water treatment, soap and detergent manufacturing, and as a drain opener.
Caustic Soda holds a crucial role in froth flotation as a modifier. In the context of mineral processing, caustic soda acts to modify the surface properties of minerals, influencing their interactions in the flotation process. This modification enhances the efficiency of froth flotation, a widely employed method for separating valuable minerals from ore. By altering the characteristics of mineral surfaces, caustic soda aids in the selective flotation of target minerals, contributing to the extraction of valuable resources from raw ore materials.
Sodium Metabisulfite (MBS), also known as Sodium disulfite, is the sodium salt of disulphurous (pyrosulfurous) acid. As a mining chemical, it occurs naturally or can be manufactured in labs. Widely recognized for its versatility, sodium metabisulfite is a key additive in various food products and wines, serving as an effective preservative. With the chemical formula Na2S2O5, this inorganic compound is sometimes referred to as sodium metabisulfite. Beyond its applications in the food industry, sodium metabisulfite finds use as a disinfectant, antioxidant, and preservative agent. When dissolved in water, it forms sodium bisulfite, and its anion metabisulfite consists of an SO2 group linked to an SO3 group, with the negative charge more localized on the SO3 end.
In froth flotation, sodium metabisulfite (MBS) proves to be a crucial chemical with multiple functions. Particularly effective for pH regulation in the froth flotation process, MBS plays a role in preventing pyrite depression. It is also instrumental in avoiding sphalerite flotation resulting from copper activation and countering the impact of Tennantite/Covellite presence in the ore. The versatility of sodium metabisulfite in addressing various challenges in froth flotation underscores its significance in mineral processing. Understanding its importance, JAM Group Co. offers sodium metabisulfite in various grades and purities, ensuring customers access a dependable and efficient chemical for their mineral processing needs.
Sodium Sulfite (sodium sulphite) is an inorganic compound represented by the chemical formula Na2SO3. As a white and water-soluble solid, it serves various industrial purposes. Commercially, sodium sulfite is employed as an antioxidant and preservative. Its utility extends to the softening of lignin in the pulping and refining processes of wood and lignocellulosic materials. While a heptahydrate form exists, it is less favored due to its heightened susceptibility to oxidation by air.
In the domain of mineral processing, sodium sulfite emerges as a crucial chemical, particularly in froth flotation applications. Its significance lies in its role as a pyrite depressant in the separation of sphalerite and pyrite through flotation. This is particularly relevant in complex ores containing minerals such as enargite and chalcopyrite. Sodium sulfite also exhibits effectiveness in influencing the surface wettability and floatability of chalcopyrite and molybdenite. JAM Group Co. is aware of its significance in mineral processing and offers the substance in various grades, ensuring different levels of purity to meet the specific needs of its customers in diverse applications.
Sodium Silicate, encompassing various chemical compounds with formulas like Na2xSiyO2y+x or (Na2O)x·(SiO2)y, includes notable examples such as sodium metasilicate (Na2SiO3), sodium orthosilicate (Na4SiO4), and sodium pyrosilicate (Na6Si2O7). These compounds typically appear as colorless, transparent solids or white powders, displaying solubility in water to varying degrees. Ranging from glassy to crystalline solids, sodium silicates are stable in neutral and alkaline solutions, but in acidic environments, the silicate ions react with hydrogen ions, forming silicic acids that may decompose into hydrated silicon dioxide gel. This chemical versatility makes sodium silicate a key substance with applications extending beyond mineral processing.
In froth flotation, sodium silicate assumes a crucial role as a modifier reagent. Widely utilized in flotation processes, it functions as a depressant or dispersant. Sodium silicate is particularly notable for its role in depressing silicate gangue, especially in systems employing carboxylic collectors. As a modifier, it contributes to the optimization of mineral separation by influencing the surface properties of minerals, aiding in the selective flotation of valuable minerals while minimizing interference from undesired gangue components. JAM Group Co. acknowledges the vital role of sodium silicate in mineral processing. The company provides this essential chemical in a range of grades and varying levels of purity, ensuring a tailored approach to meet the distinct needs of its customers in the mineral processing industry.
Zinc sulfate monohydrate, represented by the chemical formula ZnSO4·H2O, is a white crystalline compound containing zinc, sulfur, oxygen, and water molecules. This chemical is integral to the mineral processing industry, specifically in froth flotation. In the flotation process, zinc sulfate monohydrate plays a crucial role in selectively separating minerals based on their inherent properties, thereby enhancing the efficiency of mineral extraction. Its solubility in water allows for effective application, either through soil absorption or as a foliar spray, making it advantageous in agricultural settings as well. Recognizing its significance, JAM Group Co. offers zinc sulfate monohydrate in various grades, ensuring accessibility to customers worldwide and catering to the diverse needs of the mineral processing sector.
Methyl Isobutyl Carbinol (MIBC), a liquid derivative of acetone, holds a pivotal role in mineral processing, particularly in froth flotation. With limited solubility in water yet miscible with most organic solvents, MIBC functions as a crucial “frother” in the flotation process. Widely employed in the mineral industry, MIBC offers distinct advantages over other frothers, characterized by its rapid kinetics, exceptional selectivity, and the formation of dry but easily breakable froths. These attributes contribute significantly to both the yield and efficiency of mineral and metal recovery processes. JAM Group Co. provides this substance in various grades, ensuring accessibility for customers globally and meeting diverse requirements in the mineral processing field.
Sodium Isopropyl Xanthate (SIPX), known by its chemical formula (CH3)2CHOCSSNa, is an industrial chemical encompassing carbon, hydrogen, oxygen, sulfur, and sodium. Present as a water-soluble, pale yellow powder, SIPX plays a pivotal role in mineral processing, particularly in froth flotation within the mining industry. Functioning as a selective collector, SIPX is adept at separating hydrophobic materials through the formation of insoluble compounds with metallic ions. Widely used as a flotation reagent, SIPX proves invaluable in the intricate process of froth flotation, where it facilitates the separation of hydrophobic and hydrophilic materials. JAM Group Co. offers this substance in diverse grades, ensuring accessibility for customers globally and addressing the varied needs of the mineral extraction sector.
Potassium Butyl Xanthate (PBX), characterized by the molecular formula C5H9KOS2, presents as a light-yellow powder or pellet with a distinct odor, demonstrating solubility in water and rapid dissolution under acidic conditions and elevated temperatures. JAM Group Co. offers PBX in various grades, with different amounts of purities, catering to the diverse needs of its global clientele. This chemical serves as a cost-effective and potent collector in the flotation treatment of sulfide multi-metallic ores, particularly in natural circuits for copper ores and pyrite.
Potassium amyl xanthate (PAX), denoted by the chemical formula CH3(CH2)4OCS2K, stands as a pale-yellow powder with a discernible odor, showcasing its water solubility. JAM Group Co. provides PAX in diverse grades, ensuring varying levels of purity to meet the specific needs of its global customers. Widely employed in the mining industry, PAX plays a crucial role in the froth flotation process for ore separation. Particularly, it finds extensive use as a collector in both bulk and selective flotation of sulfide ores, often in conjunction with sodium isobutyl xanthate (SIBX).
Functioning as a thiol xanthate collector, PAX is strategically combined with other thiol collectors like Dithiophosphates (DTP) and Dithiocarbamates (DTC) to enhance selectivity in the extraction process. Noteworthy applications include efficient nickel extraction, where studies have highlighted PAX and its mixtures achieving the highest cumulative nickel grades. Its versatility extends to serving as a collector for metallic ores, a flotation reagent, and a surface-active agent, underscoring its significance in mineral processing.
JAM Group Co., as an Iran supplier of Potassium Amyl Xanthate PAX, understands the importance of timely and efficient delivery of their mineral processing chemicals. That’s why we have invested in state-of-the-art packaging and logistics solutions to ensure that the products reach our customers in perfect condition and on schedule. The company’s advanced packaging methods make it a powerful Iran trader of potassium butyl xanthate PBX (so-called Производитель амилксантогената калия PAX in the Russian language). As such, customers can be confident that their products will be protected during transportation, no matter how far they need to travel.
In addition to our top-notch packaging, we also boast an efficient shipping operation that contributes to our reputation as an Iran exporter of sodium isopropyl xanthate (SIPX). At JAM Group, we’ve established strong relationships with global shipping providers, allowing us to offer competitive rates and quick delivery times. This means that customers worldwide can count on JAM Group Co. to supply them with their necessary mineral processing chemicals in a timely and cost-effective manner, regardless of whether they’re searching for Sodium Isopropyl Xanthate (SIPX) price, Potassium Butyl Xanthate PBX price, or Potassium Amyl Xanthate PAX price. With our company’s ability to deliver each mineral processing chemical, we can accommodate the needs of customers from all sectors.
Copyright © 2024 Jam Group Company. All rights reserved.